Quality
Policy
The SG Holdings Group believes that quality underlies safe and secure services. To deliver service quality responding to the trust of customers and employees, we are establishing systems and mechanisms that improve quality according to the characteristics of each Group company.
Systems
The Group has built quality management systems to match the characteristics of each Group company. For example, Sagawa Express, which is the core of the Group, has established a Quality Assurance Department in its head office, and also appointed quality managers at its branches and sales offices nationwide. These officers work on maintaining and inproving quality by periodically checking quality standards.
Initiatives
Achievement of Goals and Compliance with Rules (Sagawa Express)
Sagawa Express conducts quality management based on ISO 9001. The company has established the five quality items below, and each month it tracks numerical targets for each branch office and sales office for response quality and unified nationwide for freight quality and time quality. In the event a problem arises with these quality items, this is shared across branches and sales offices in the weekly companywide morning meeting to ensure action is taken immediately. Internal audits of all sales offices in Japan are conducted annually to check about 60 items. We currently have approximately 3,000 internal auditors who hold internal qualifications.
Response quality | (1) Rate of occurrence of claims (related to response) |
---|---|
(2) Rate of occurence of claims (other) | |
Freight quality | (3) Rate of occurrence of outbound freight accidents |
(4) Rate of occurrence of arriving freight accidents | |
Time quality | (5) Morning commercial delivery rate |
Frequency | Name | Purpose | Participants and Personnel in Charge | |||
---|---|---|---|---|---|---|
Head office | Branches | Sales Offices | Internal Auditors | |||
Weekly | Quality report at companywide morning meeting | Report the state of achievement of quality items. Immediately respond if there are any problems. | Directors General Managers | Branch Managers | Sales Office Managers | |
Monthly | Nationwide Branch Manager Meeting | Report the state of achievement of quality items. Immediately respond if there are any problems. | Directors General Managers | Branch Managers | Sales Office Managers | |
Annually | Internal audit | Check quality of about 60 items in all sales offices nationwide. Internal auditors are qualified personnel within the company (approximately 3,000 qualified employees) | yes |
Mechanisms for Fully Applying Customer Feedback (Sagawa Express)
Sagawa Express has established a Customer Service Sections in each of its sales offices to create a system for swiftly responding to requests from customers. Furthermore, comments and requests made by customers via the Website or over the telephone are utilized by the Quality Assurance Department in Head Office in order to improve customer satisfaction.
Forklift Operation Skills Contest (Sagawa Global Logistics)
Sagawa Global Logistics, which operates a logistics business, holds a Forklift Operator Skill Contest. The aim of this contest is to improve the safety awareness, operating skills and inspection skills of forklift operators.
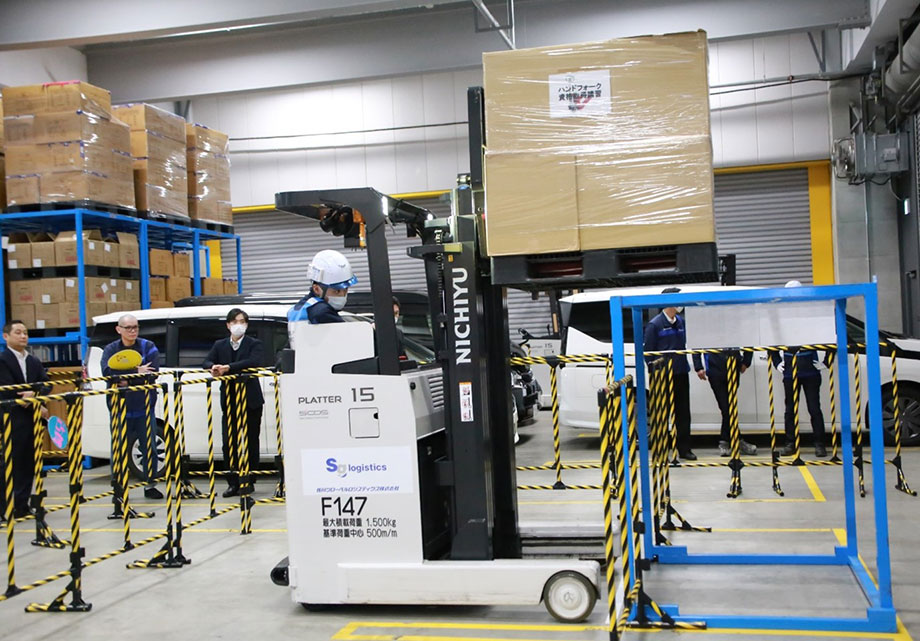
Providing Safe and Secure Services